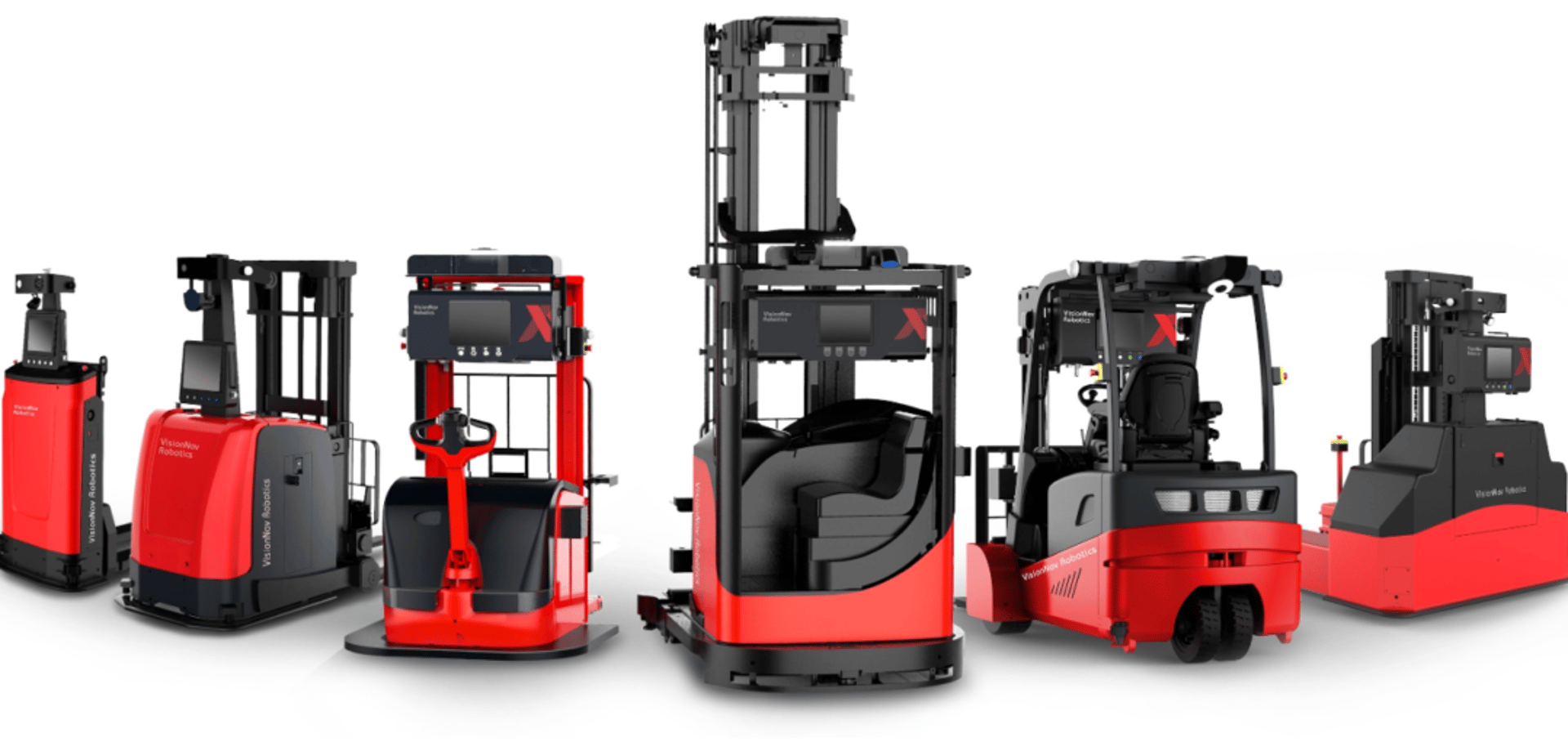
AGV Robot
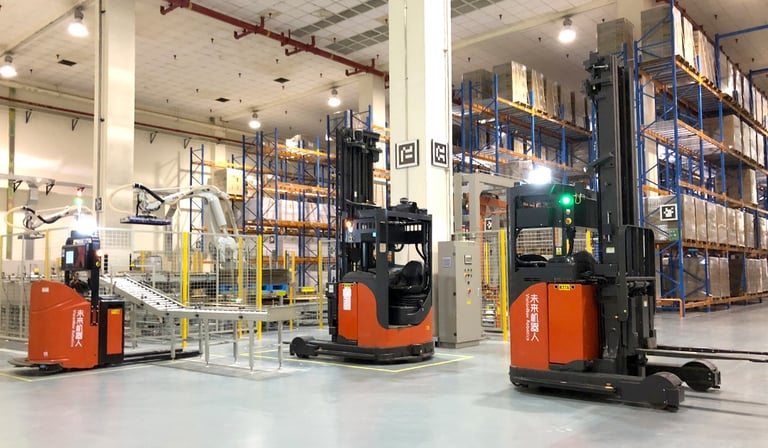
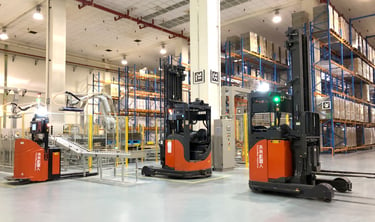
AGV (Automated Guided Vehicle) robots are designed to autonomously transport goods within a warehouse setting. These robots utilize advanced vision and navigation technologies to efficiently move items from one location to another.
AGVs employ path planning algorithms to determine the most efficient routes for transporting goods within a facility. The load handling mechanism is designed to securely transport items of various shapes and sizes. Besides, AGV robot determine their precise location within the warehouse, ensuring accurate movement and positioning during transportation tasks.
Goods Transport
VisionNav AGV’s work on hundreds of facilities across the world, providing over 11m pallet storages, narrow-aisle operations, automated truck loadings, multi- layer cage stackings and other fully autonomous actions.
Other than that, the AGV robot uses precise positioning systems using 3D cameras and sensors, to align itself accurately with the target pallets for stacking. Also, the AGV’s path planning algorithm is designed to calculate optimal routes for approaching, lifting, and stacking pallets in a multi-layer configuration.
Multi-layer Stacking
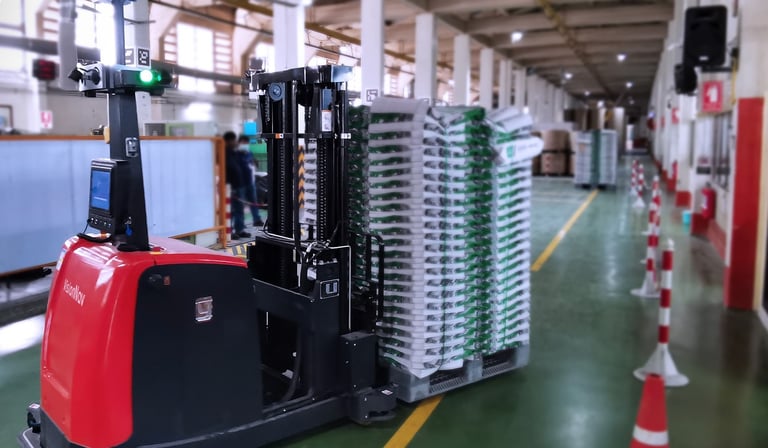
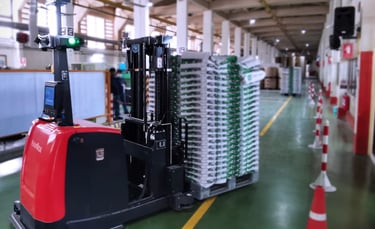
AGV robot is programmed to navigate to specific pick-up points for loading and drop-off points for unloading. It is equipped with load handling mechanisms, such as forks, conveyor systems, or robotic arms, to pick up and carry goods.
Good things, the mechanism is designed to securely hold and release the load during loading and unloading operations. AGVs may communicate with other automated systems, such as conveyor belts or robotic arms at loading/unloading stations. This communication facilitates seamless transfer of goods between different parts of the warehouse.
Loading and Unloading
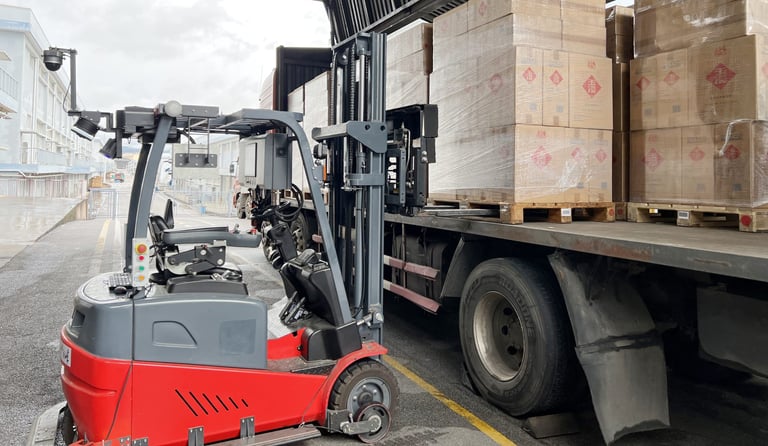
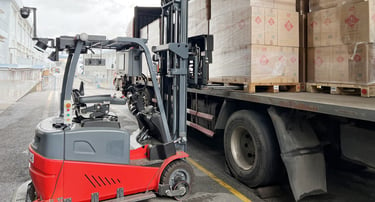
© 2024 T-Robot. All Rights Reserved.